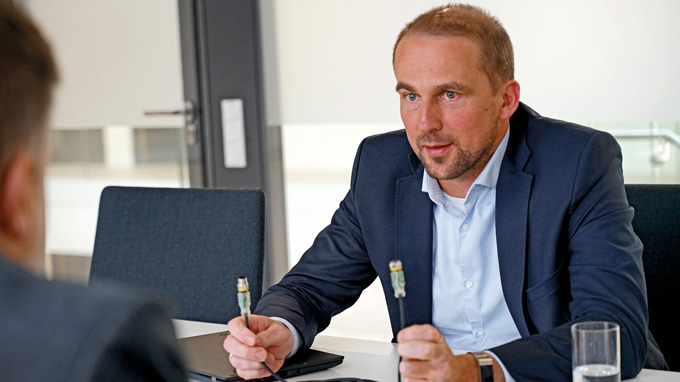
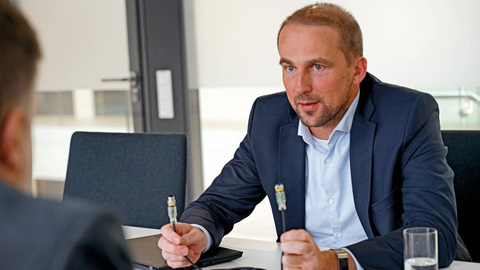
Product manager Alexander Ix explains the functions and advantages of Turck's M12Plus connectors
Reliable Real-time Monitoring of Sensor-Actuator Cables
To enable condition monitoring of sensor-actuator cables, Turck is equipping the new M12Plus connectors with voltage and current monitoring electronics as well as a Bluetooth chip that can transmit the measured values to a controller. This means that the condition of the cables can be continuously monitored in order, if necessary, to intervene in good time, says product manager Andreas Ix in an interview with Michael Corban, editor-in-chief of the trade journal KEM Konstruktion|Automation.
You have packed a Bluetooth transmitter into the connector – what‘s the idea behind that?
Our new M12Plus connectors are a pure, technology-driven development. The basic idea is to move the condition monitoring of highly stressed cables directly to the connection technology. We have integrated the necessary voltage and current monitoring electronics as well as a Bluetooth chip into the connector. In this way, the measured voltage and current values can be sent wirelessly to a controller continuously – currently once a second – or an alarm can be triggered depending on the application.
What happens to the measured values?
The information obtained is available directly and easily at the automation level via the Bluetooth connection to our IP67 PLC TBEN-PLC, for example. They can not only be individually pre-processed, evaluated and visualized here, but also ex-changed with all other participants via multiprotocol. What‘s more, the TBEN-PLC also enables the condition values of the line to be transferred directly to the cloud if required, which supports IIoT applications. The Cable Monitor app in our Turck Automation Suite (TAS) can also be used in parallel. By comparing input and output values, problems such as cable kinks, cable breaks or power supply loss are detected early on, making it much easier to implement condition monitoring and predictive maintenance of the cables. This is a tremendous benefit, especially for applications with drag chains or in robotics.
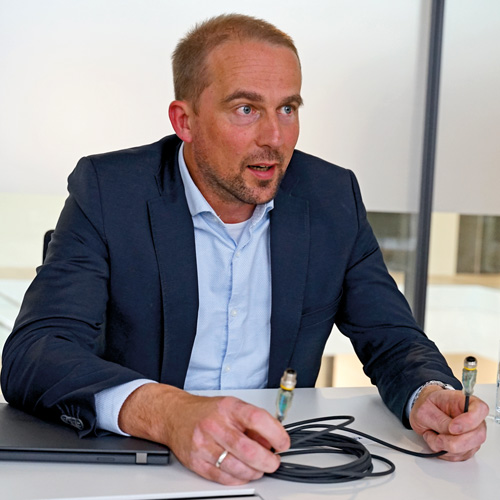
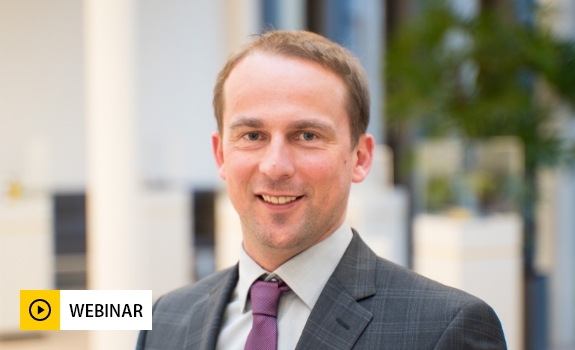
Can individual cables also be uniquely identified via the connectors?
Yes, because in most cases several cables will be used. To do this, we can parameterize the connectors and assign a unique ID to each cable. This offers a number of benefits: The user can identify in advance any cable that is at risk of failure via the individual MAC address of each connector and replace it immediately. A QR code on the connector will make maintenance even easier.
So the condition of the cables can be monitored – has monitoring of the connected actuators also been considered? For example, via the current and voltage values of a connected motor?
Our main focus is currently on monitoring the cables – but in principle it is possible to extend this to the connected devices. An application has already been implemented for preventing the unintentional shutdown of a conveyor system. The M12Plus cables with integrated condition monitoring detect increasing current consumption of stopper motors and report this to the PLC via Bluetooth. The stoppers are designed to prevent material jams. However, the drives get dirty quickly and then no longer work correctly, resulting in the motor drawing more current. If a threshold value is exceeded, the safe shutdown of the conveyor system is triggered and maintenance can rectify the problem. This example illustrates the advantage of our technology-driven approach: Although the focus is initially on the cable and its condition, a variety of other applications can be implemented. We are always open to exciting new ideas.
Compared to a standard sensor-actuator cable: How much more expensive is the variant with the M12Plus connectors compared to the standard cable?
Of course, the smart connectors have to be more expensive, but the user still benefits because their use can prevent machine downtime, for example. The costs incurred in the event of an unplanned production shutdown would be much more relevant here. The following must also be taken into account: As the saying goes, contacts are the end of electrical engineering. In fact, the most common causes of faults are poor plug connections or a faulty cable. Both – including the quality of the plug connection – can now be monitored, as products such as M12Plus and the TBEN portfolio complement each other perfectly. This is a particular benefit with regard to IP67 technology. It offers immense advantages, but a major disadvantage is the time-consuming troubleshooting. While the voltage can be easily measured at a terminal in the control cabinet, this has so far involved considerable effort
in the plug connector. This is now much easier with our solution.
What goals is Turck generally pursuing in the field of connection technology?
We are constantly expanding our extensive portfolio in this area – which includes couplings and connectors, flanges and bushings, connecting cables and fieldbus cables and distributors in numerous designs. Self-assembly plug connectors are also available. The range also includes inductive couplers – for example, the contactless inductive couplers in the NIC series transmit up to 16 switching signals via IO-Link and up to 18 W of power if required.
Author | The interview was conducted by Michael Corban, editor-in-chief of the trade journal KEM Design|Automation
Select Country
Turck worldwide